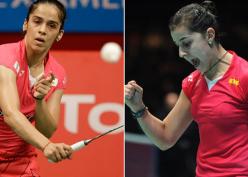
সিন্ধুর পর মারিনের কাছে হারলেন সাইনাও
সিন্ধুর পর মারিনের কাছে হারলেন সাইনাও
January 3, 2017, 11:30am
খেলা
অপ্রতিরোধ্য ক্যারোলিনা মারিন৷ ভারতের মাটিতে ভারতীয় ফ্র্যাঞ্চাইজি দলের হয়ে খেলছেন তিনি৷ অথচ ভারতের সেরা ব্যাডমিন্টন তারকারাও তাঁকে রুখতে পারছেন না৷ বছরের প্রথম দিনই রিও অলিম্পিকে রুপো জয়ী পি ভি সিন্ধু হার মেনেছিলেন৷ সোমবার মারিনের কাছে পরাস্ত হলেন সাইনা নেহওয়াল৷প্রিমিয়ার ব্যাডমিন্টন লিগে (পিবিএল) এদিন আওয়াধে ওয়ারিয়র্সের হয়ে কোর্টে নেমেছিলেন বিশ্বের প্রাক্তন এক নম্বর সাইনা৷ লক্ষ্য ছিল একটাই৷ মারিনকে মাটি ধরিয়ে হায়দরাবাদকে চাপে ফেলা৷ কিন্তু বাস্তবে তেমনটা হল না৷ সিন্ধুর বিরুদ্ধে জিততে হাড্ডাহাড্ডি লড়াই করতে হয়েছিল স্প্যানিশ শাটলারকে৷ কিন্তু সাইনাকে স্ট্রেট গেমে উড়িয়ে দিলেন তিনি৷ মারিনের পক্ষে খেলার ফল ১৫-১৪, ১১-৫৷পিবিএল-এর প্রথম দিন সিন্ধুর চেন্নাইকে ৪-৩ ব্যবধানে হারিয়ে স্বস্তিজনক জায়গায় রয়েছে মারিনের হায়দরাবাদ৷ এদিন তিনি হারিয়ে দিলেন সাইনাকে৷ চোট সারিয়ে কোর্টে ফেরার পর থেকে নিজের সেরা ফর্মে পাওয়া যায়নি হায়দরাবাদি শাটলারকে৷ নতুন বছরে তাই ঘুরে দাঁড়াতে মরিয়া তিনি৷
- আইসিসি-র-বর্ষসেরা-টেস্ট-দলে-নে
- যুব-বিশ্বকাপের-ফাইনাল-পেল-যুবভ
Comments
Vibration Diagnostics: A Comprehensive Guide to Dynamic Shaft Balancing
Vibration diagnostics is a crucial process in maintaining the efficiency and longevity of rotating machinery. This technique allows for the identification and rectification of issues associated with unbalanced rotors, which can give rise to excessive vibrations and operational problems. Central to vibration diagnostics is dynamic shaft balancing, an essential technique utilized across various industries to enhance the performance of machines, including fans, turbines, and crushers.
Understanding Vibration Diagnostics
Vibration diagnostics refers to the process of measuring and analyzing the vibrations produced by machinery during operation. It provides invaluable insights into the condition of rotating components, helping to detect issues before they escalate into serious problems. One of the primary goals of vibration diagnostics is to achieve optimal balance in rotating parts to minimize vibrations and wear. In this context, it is vital to distinguish between static and dynamic balance.
Static vs. Dynamic Balance
Static balance occurs when the center of gravity of an object is aligned with its axis of rotation. In a state of static imbalance, the rotor sits unevenly, causing one side to experience a downward pull due to gravity. This imbalance can typically be corrected by adding or removing mass at designated locations on the rotor??™s surface.
Dynamic balance, on the other hand, involves more complex scenarios where the rotor experiences imbalances in different planes during rotation. When the rotor is dynamically unbalanced, it produces centrifugal forces that do not adequately compensate for each other due to varying mass distributions along its length. It requires advanced techniques for correction, typically involving the use of sophisticated gadgets like vibration analyzers and balancers.
The Dynamic Shaft Balancing Process
Dynamic shaft balancing is performed using specialized devices such as the Balanset-1A. This portable balancer enables technicians to analyze and balance rotors with precision, covering a wide array of applications. The process involves several systematic steps:
1. Initial Vibration Measurement
The balancing process begins by mounting the rotor on a balancing machine. Vibration sensors are attached to the rotor, and the rotor is operated to measure initial vibrations. This data serves as a benchmark for subsequent evaluations and corrective measures.
2. Calibration and Measurement Adjustments
Next, a calibration weight is installed on one side of the rotor to observe its effects on vibration. After securing the weight, the rotor is run again to measure changes in vibration. This process helps determine how the added mass influences the rotor's balance, contributing vital information towards achieving dynamic equilibrium.
3. Iterative Adjustments
The calibration weight is moved to other points on the rotor, and vibrations are measured again. Multiple measurements capture how different placements impact the rotor's performance. This iterative adjustment is critical for developing an accurate understanding of where corrective weights should be installed for optimal balance.
4. Final Weight Installation and Balance Verification
Once all necessary data is collected, the balance analyzer computes the required angles and masses for corrective weights. These weights are affixed at specific points indicated by the analysis. Following their installation, the rotor is started once more to ensure that vibration levels have significantly decreased, confirming the effectiveness of the balancing process.
Importance of Correct Weight Placement
Correct weight placement is paramount in the dynamics of vibration diagnostics. Each adjustment made during the balancing process hinges on precise angle measurements, ensuring that the weights counteract any generated torque from the unbalanced masses. The fundamental relationship is defined through the interaction of trial weight positions and any necessary corrective weights, which must be installed at calculated angles based on the rotor??™s direction of rotation.
Applications of Vibration Diagnostics in Industry
Dynamic shaft balancing has diverse applications across sectors, including manufacturing, aerospace, and automotive. In manufacturing industries, it ensures that machinery, such as crushers and augers on combines, operates smoothly, reducing the risk of breakdowns. In the aerospace sector, maintaining balanced turbofans and turbines is critical for performance and safety. Likewise, the automotive industry benefits from vibration diagnostics by optimizing component performance, reducing wear, and enhancing vehicle reliability.
Conclusion
In summary, vibration diagnostics is an essential practice for diagnosing and correcting imbalances in rotating machinery. Through dynamic shaft balancing, industries can ensure optimal machinery performance, reduce the potential for unexpected downtime, and extend the lifespan of equipment. Utilizing devices like the Balanset-1A facilitates accurate diagnostics and fosters a proactive approach to equipment maintenance, ultimately contributing to improved operational reliability and efficiency.
Vibration monitoring equipment is essential for industries that rely on machinery and rotors for their operations. The Balanset-1A is a portable balancer and vibration analyzer specifically designed for dynamic balancing in various applications, including crushers, fans, mulchers, augers, shafts, centrifuges, and turbines. With its innovative design and dual-channel capability, this equipment enhances operational efficiency and helps maintain machinery in optimal condition.
The Balanset-1A is not just a simple monitoring device; it encompasses a variety of features that make it versatile for multiple industries. Its ability to provide precise measurements in two different planes makes it ideal for diagnosing and mitigating vibration issues. By enabling dynamic balancing, this equipment decreases vibration levels, thus prolonging the lifespan of machinery and minimizing maintenance costs.
This vibration monitoring equipment comes with various functionalities tailored to facilitate rotor balancing and vibration analysis. The Vibrometer mode allows users to accurately measure rotational speed (RPM) and determine the phase angle of the vibration signal. It also analyzes the fundamental frequency component and provides a detailed FFT spectrum analysis??”essential for understanding complex vibration patterns and their implications.
One of the standout features of the Balanset-1A is its Balancing mode capabilities. It supports both single-plane and two-plane balancing, enabling detailed adjustment to achieve dynamic balance. This feature is particularly beneficial for industries dealing with multiple rotor types, as it allows for thorough analysis and correction tailored to specific machinery. Additionally, the polar graph functionality visually represents imbalances, making it easier to identify the necessary adjustments and placement of weights during the balancing process.
Another vital aspect of this vibration monitoring equipment is its ability to log measurements. This feature stores data for future reference, enabling businesses to track their machinery??™s performance over time and review any alterations in vibration levels or rotor balance. The built-in tolerance calculator ensures that industrial standards, such as ISO 1940, are maintained, further assisting in the accurate balancing of rotors.
The Balanset-1A not only provides essential measurements and charts for detailed analysis but also offers historical archive capabilities. This allows users to store and easily access past balancing sessions, generating comprehensive reports that evaluate the efficiency of balancing procedures and any necessary adjustments moving forward. Re-balancing is also made easy with the equipment??™s capability to revisit saved data and repeat the balancing process as required.
Designed to handle both standard and specialized balancing tasks, the Balanset-1A is equipped with essential components, including two vibration sensors, an optical sensor (laser tachometer), and a USB interface for software connectivity. These components ensure that users have comprehensive data necessary for effective vibration monitoring and analysis.
The operating specifications of this vibration monitoring equipment are tailored for efficiency. The device is capable of measuring a wide range of vibration velocity, ensuring that it can adapt to different machinery requirements. Additionally, it operates across various RPM ranges, extending its usability to different types of industrial rotors. The accuracy of the device is high, with allowances for measurement error, contributing to reliable and effective vibration analysis.
For industries looking to enhance their machinery's performance, investing in vibration monitoring equipment such as the Balanset-1A is crucial. The integration of advanced technology within this system not only simplifies the balancing process but also provides actionable insights into machinery health. Keeping machinery maintained enhances operational efficiency, minimizes downtime, and ultimately leads to cost savings.
Furthermore, the Balanset-1A is user-friendly, supporting different measurement systems, which means it can be utilized globally regardless of regional standards. This flexibility makes it an ideal choice for companies operating on an international scale or managing diverse machinery types across various locations.
Lastly, the importance of vibration monitoring equipment cannot be overstated. As machinery operates, vibrations are inevitable; however, excessive vibrations can lead to equipment failure, accidents, or more serious operational disruptions. By regularly measuring and balancing rotors with devices like the Balanset-1A, industries can not only enhance their machinery performance but also ensure a safer workplace.
As a conclusion, whether working with crushers, centrifuges, or turbines, ensuring that machinery operates smoothly is paramount. The Balanset-1A is at the forefront of vibration monitoring equipment, offering comprehensive features that suit various industries. The ability to perform dynamic balancing effectively and analyze vibration patterns ensures that any potential issues can be identified and resolved swiftly. This equipment not only optimizes production processes but also secures investments in machinery, leading businesses to greater efficiency and productivity.
Article taken from https://vibromera.eu/